Az IoT és az „adatforradalom” nagyban segíti a gyártóvállalatokat is, hasonlóan más olyan iparágakhoz, mint pl. a telekommunikáció és a retail. A gyártó cégek az optimalizálási potenciált az adatokban és az ehhez szükséges „intelligenciában” keresik; a termelés hatékonyabbá tételével, a hulladék csökkentésével, más szóval a lean manufacturing támogatásával.
Gondoljunk csak a mai technológiai fejlettségre a gyártásban, a Ford T-modell idejéhez képest. Számos gép automatizált, míg legtöbbjük adatgyűjtést is végez. És mégis, a gyárakban lévő gépek kevesebb mint 5%-át monitorozzák valós időben. Ez hatalmas akadálya a teljes transzparenciának.
Az adatok értékének és a benne foglalt információknak a becslése elengedhetetlen annak eldöntéséhez, hogy melyik projektet kell végrehajtani az Ipar 4.0 átalakítások során. Lássuk a főbb megközelítéseket, amelyek segítségével meghatározható egy szervezeten belül az adatok értéke.
Módszerek az adatok értékének mérésére:
- Az előnyök monetizációs megközelítése: az adatok értékét az egyes adattermékek előnyeinek meghatározásával, majd az előnyök monetizálásával becsüljük meg. Például a gép időről időre elkezd hibás termékeket gyártani, jelentős működési állapotváltozás nélkül. Ha ez megtörténik, a gépet 20-30 percig leállítják, és a szerszámokat megtisztítják. Ha a hibás elemek keletkezését előre lehetne megjósolni, az operátorok elkerülhetnék a problémát. Ez naponta 1 órás gépi időt takarít meg, és kb. 50 hibás terméket. Ebben a példában a gép adatait használjuk fel a nem kívánt események előrejelzésére, beavatkozásuk elkerülésére és mérhető előnyök létrehozására.
- Hatás alapú megközelítések: itt az értéket az adatok rendelkezésre állásának gazdasági és társadalmi eredményekre gyakorolt okozati hatás értékelésével határozzuk meg, még a szervezeten belül is. Ebbe a kategóriába tartoznak a napi munka hatékonyságát növelő és a munkavállalók frusztrációjának csökkentését elősegítő (feldolgozott) adatok is. Például, ha az ismétlődő, unalmas munka automatizálható, akkor a munkavállalók és az elemzők több hozzáadott értékkel és boldogabb érzéssel tudnak dolgozni.
A fentieken kívül több más megközelítés is létezik (pl. költségalapú, piaci alapú, jövedelemalapú), de a már említett kettő az, ami leginkább alkalmazható a gyártóipar számára.
Az üzleti előnyök
A legfontosabb kérdés azonban minden esetben az, hogy az adatok járnak-e mérhető és kézzelfogható üzleti előnyökkel? Az elsődleges lépés azon gyártók számára, akik szeretnék felhasználni az adataikat a hozam növelése érdekében, annak vizsgálata, hogy mennyi adat áll valójában a vállalat rendelkezésére. Hiszen a legtöbb vállalat ugyan összegyűjti a folyamatadatokat, de csak nyomkövetési célokra használja őket, nem pedig a műveletek fejlesztésének alapjául. Ezen szervezetek kihívása elsősorban az, hogy befektessenek olyan rendszerekbe és skill set-ekbe, amelyek lehetővé teszik számukra a meglévő folyamatinformációk használatának optimalizálását.
Az adatsiló probléma
Az adatok birtoklása azonban nem elég. Gyakori, hogy a vállalatok adatai külön osztályok ellenőrzése és használata alatt állnak, és az információáramlás blokkolva van. Ilyen helyzetekben az adat- vagy akár információssilókról beszélünk. Az adatsiló rögzített adatok tárolója, amely alapvetően egy osztály ellenőrzése alatt áll és elkülönül a szervezet többi részétől.
Az adatsilók hatalmas akadályt jelentenek, ha a vállalat láthatóbbá és átláthatóbbá kívánja tenni a működését. Ha észreveszi, hogy az Ön szervezetében is megtalálhatóak ezen adatsilók, érdemes megoldást keresni és hidakat építeni közöttük. Ebben az esetben megoldásként valószínűleg egy IoT platformhoz fog eljutni.
A megoldás: egy IoT platform
Egy olyan IoT platform, mint a REACH, alapvetően bármely gyár „idegrendszereként” funkcionálhat. Különböző funkcionális egységeket, gépeket és szenzorokat kapcsol össze az emberrel, mindkét irányban továbbítja a jeleket, tárolja és elemzi az adatokat, és képes bizonyos mértékig intelligenciát mutatni.
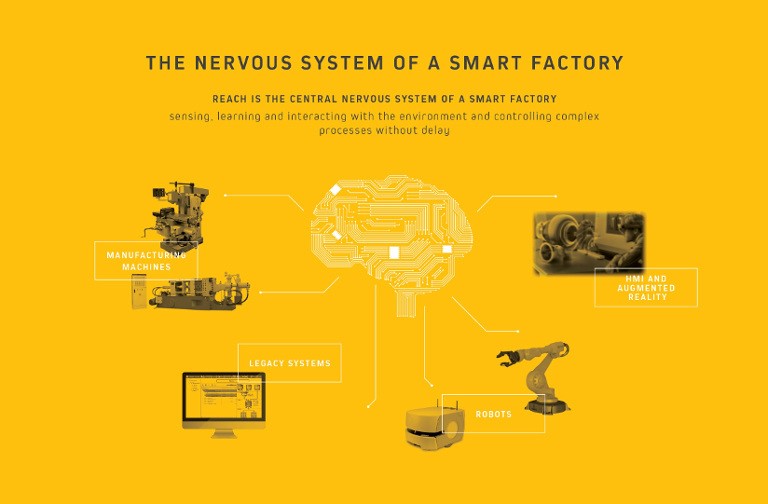
Az ehhez szükséges adatokat különböző gyártási fázisokból, területekről és gépekből szükséges gyűjteni, így a prediktív karbantartási algoritmusok felügyelhetik az egész gyártási folyamatot annak érdekében, hogy időben értesítsék a megfelelő személyzetet, amely megakadályozhatja vagy megszüntetheti a hibát. Ha szeretné elérni ezt a funkcionalitást, rendelkeznie kell egy cross-department/cross-operational IoT platformmal. Ez az integrált gépi tanulási és előrejelző karbantartási megoldás előzetes feltétele.
Van úgy, hogy csak az adatforrások között létrehozott, hiányzó kapcsolat képes hatalmas előnyt nyújtani. Képzeljük el, hogy egy összeszerelési folyamat egy lépéseként ragasztógépet használunk. A ragasztó ereje az idő függvényében változik, és nem tudjuk miért; vannak olyan napok, amikor 20 százaléknyi hibás termék keletkezik az elégtelen tapadási minőség miatt. Még ha a gépből gyűjtött adatokat is elemezzük, nincs olyan minta, amely a gépadatok és a végtermék minősége közötti ok-okozati összefüggést kimutatná. Bizonyos ponton arra jutunk, hogy a gépadatokat a gyári időjárás előrejelző készülékekkel kell összekötni, és ekkor láthatjuk, hogy a ragasztás minősége korrelál a levegő páratartalmával, így elkezdhetjük a probléma megoldását, ami jelentősen csökkentheti a hibás termékek számát.
Egy nyereséges use case megvalósítása
A mérhető üzleti előnyöket biztosító use case megvalósítása nem kizárólag az adatforrásoktól és az adatok minőségétől függ. A valós érték megteremtésének képessége a szervezeten belül rejlik, amely megfelelő módszereket igényel.